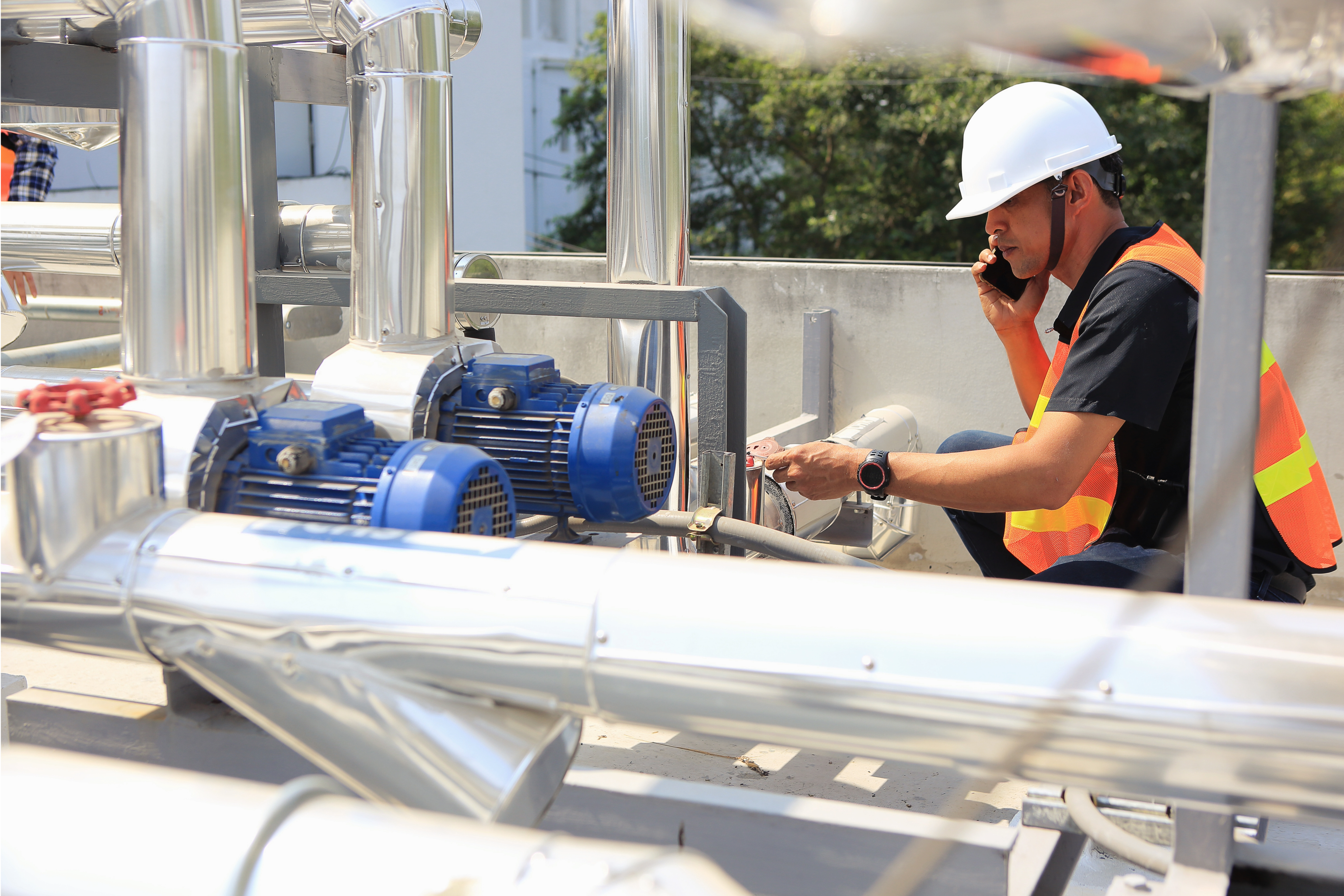
Undoubtedly, you have seen there are many different types of control valves. These can come in a variety of sizes, materials, and have a vast array of options and additions. But why so much complexity? Why so many trim options? Why have such confusing product codes detailing the exact product?
Today we will cover the basics of control valve specification and answer those questions. We will look at the considerations when choosing a valve and why complex solutions may be needed depending on process demands. For this blog, we will be focused primarily on process control valves. For that reason, we won’t be covering the actuators, assemblies, regulators, and self-contained pressure controller units that may go with them.
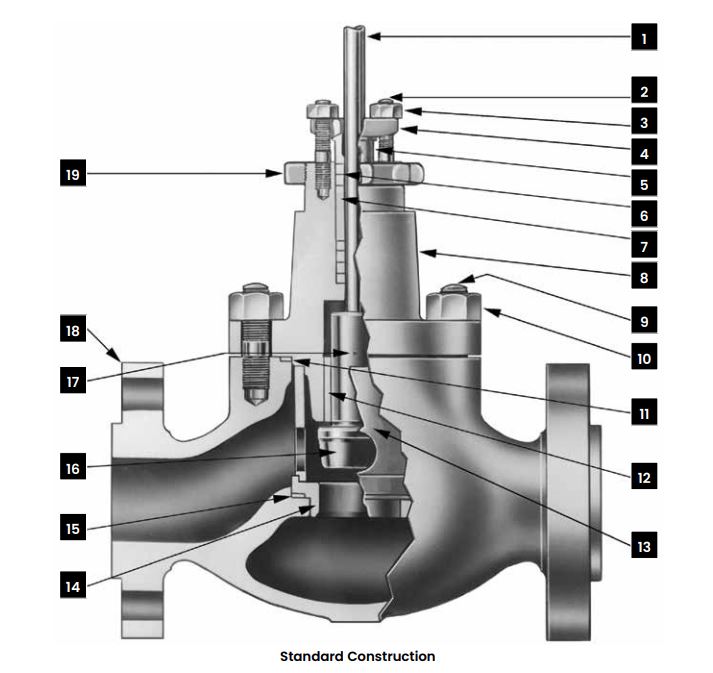
Basics of Control Valve Selection
Simply put, the control valve specified by your product specialist/engineer will be composed of the criteria your process conditions dictate. We will go through the key criteria step-by-step to discover what might be important for the proper control valve specification.
First, we’ll look at and breakdown the:
Process Fluid and Various Flow Conditions
Process Fluid Temperature – the temperature of the fluid flowing through equipment is necessary when considering what material of construction the valve should have.
Process Fluid Viscosity Range – the viscosity range of the fluid will impact the trim and material of the valve body. Viscosity is the measurement of a fluid’s resistance to shear forces. So, knowing its effects on friction and pressure drop through the valve is essential to proper operation of the desired equipment.
Pressures Within the Flow Line – We use the word “pressures” because it’s more complex than simply choosing a material to withstand the potentially high-pressure conditions of the flow. The type of valve, material, and trim options are dependent on the minimum and maximum pressure specifications at the valve’s inlet and outlet. Also to be considered is the desired/expected pressure drop across the valve body itself. These conditions must be given to the equipment manufacturer and product engineer by the client’s process engineer team. This information is critical, as pressures and pressure drop across the valve can have consequential effects on the process fluid itself.
Other Fluid Defining Characteristics – This section will be kept brief, but we will touch on the physical nature of the fluid itself. The fluid’s state, whether gaseous or liquid, will make for quite different situations. Additionally, there are many operations that will be flowing with a slurry. This is commonly found in operations like the food and beverage industry, as well as pulp and paper. Slurries can clog up and compromise the process conditions if not handled with the right process control equipment. Lastly, but of course not least, is the implication of extremely corrosive and damaging fluids. Within the oil industry, many operations require stainless steel components for this very reason. Other materials simply cannot hold up to the harsh fluids and process conditions required in this industry.
Finally, let’s touch on an example of some other options that could be included in a control valve specification. A baffle system engineered to reduce sound may be included if there are maximum noise requirements provided by the process design team. This can be in the form of the valve trim itself, or can be an additional insert that works to silence the flow as it travels through the valve cavity.
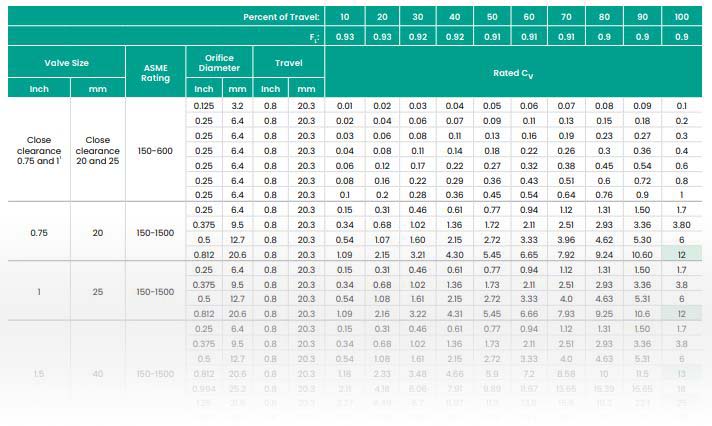
Why It Matters
As you can see, things can quickly get complicated. When the characteristics of your control solution are specifically tailored to your process conditions, it’s easy to see how product codes become long and confusing. Each option and element in the design are important to clarify and employ.
Engineers and product experts have deep experience in their domain and these products. They are constantly educating themselves on new technologies in order to provide the most up-to-date and effective solutions for their clients.
For the Future
When it comes to the process control capabilities itself, it’s going to get even more complicated. Depending on the flow characteristics needed, quick-acting, equal percentage, or linear actions can be specified.
This is where you start getting into the actuation technology section, but we promised not to get into the weeds of it today. Keep checking our blog for more information, and of course, always contact your product experts for your process control needs. They are well versed and trained in all things process controls and would be more than happy to help you out!
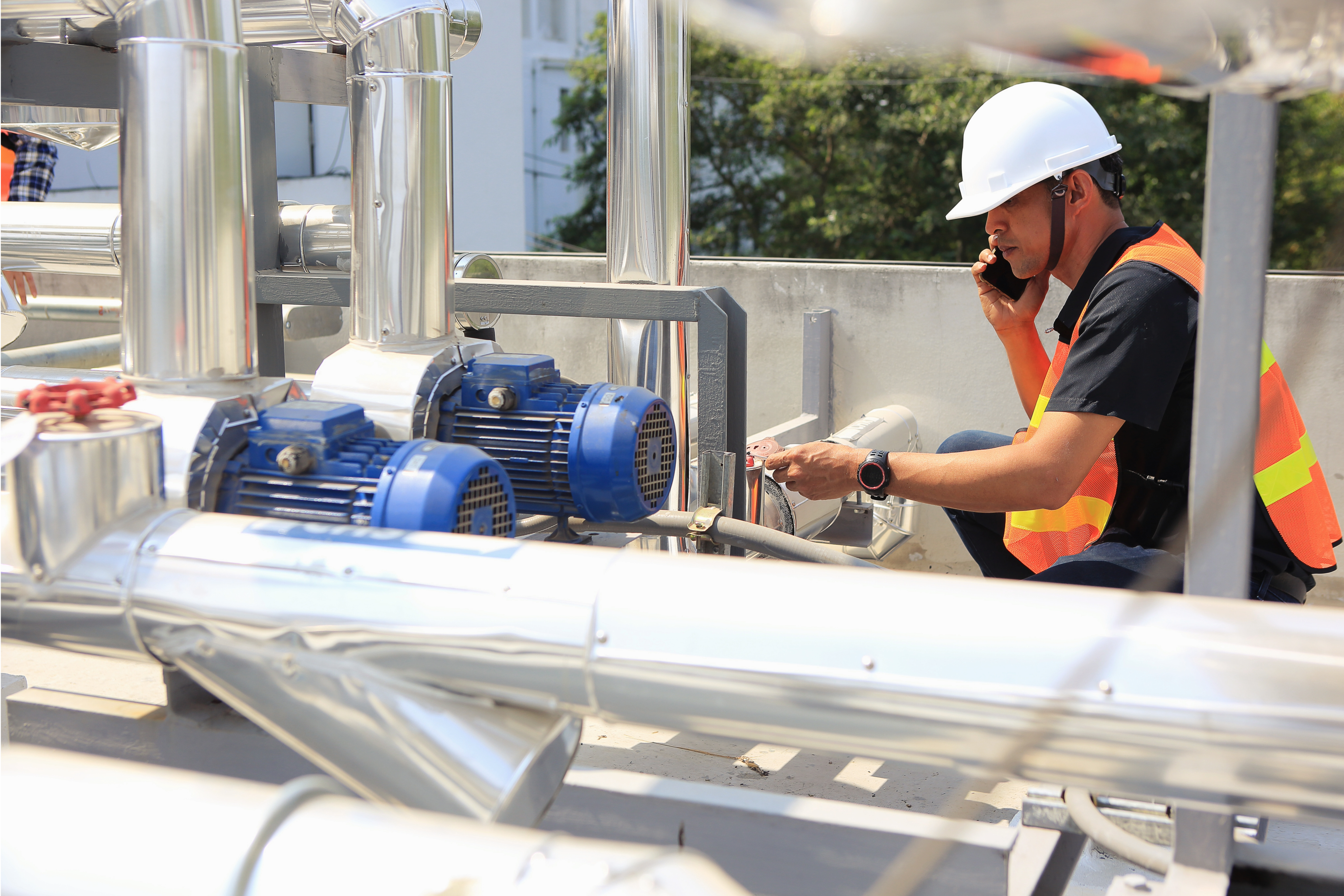
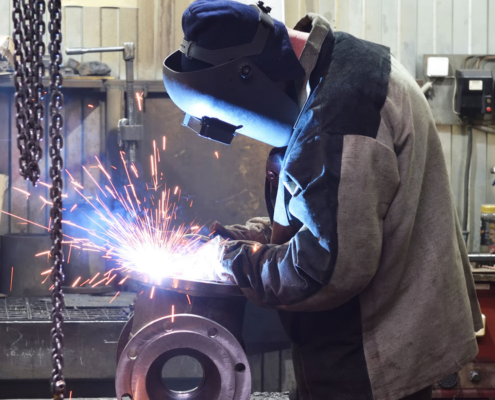
Common Control Valve Problems and How to Fix Them
Control Valves, Industrial Valves, Valve Maintenance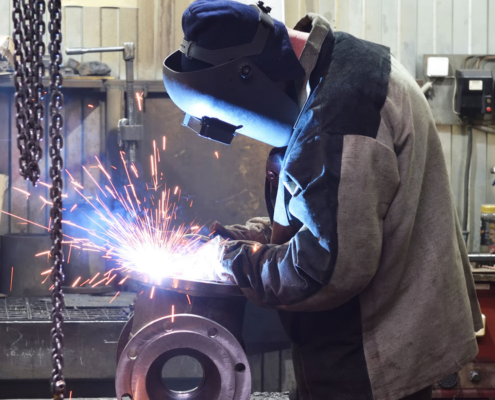