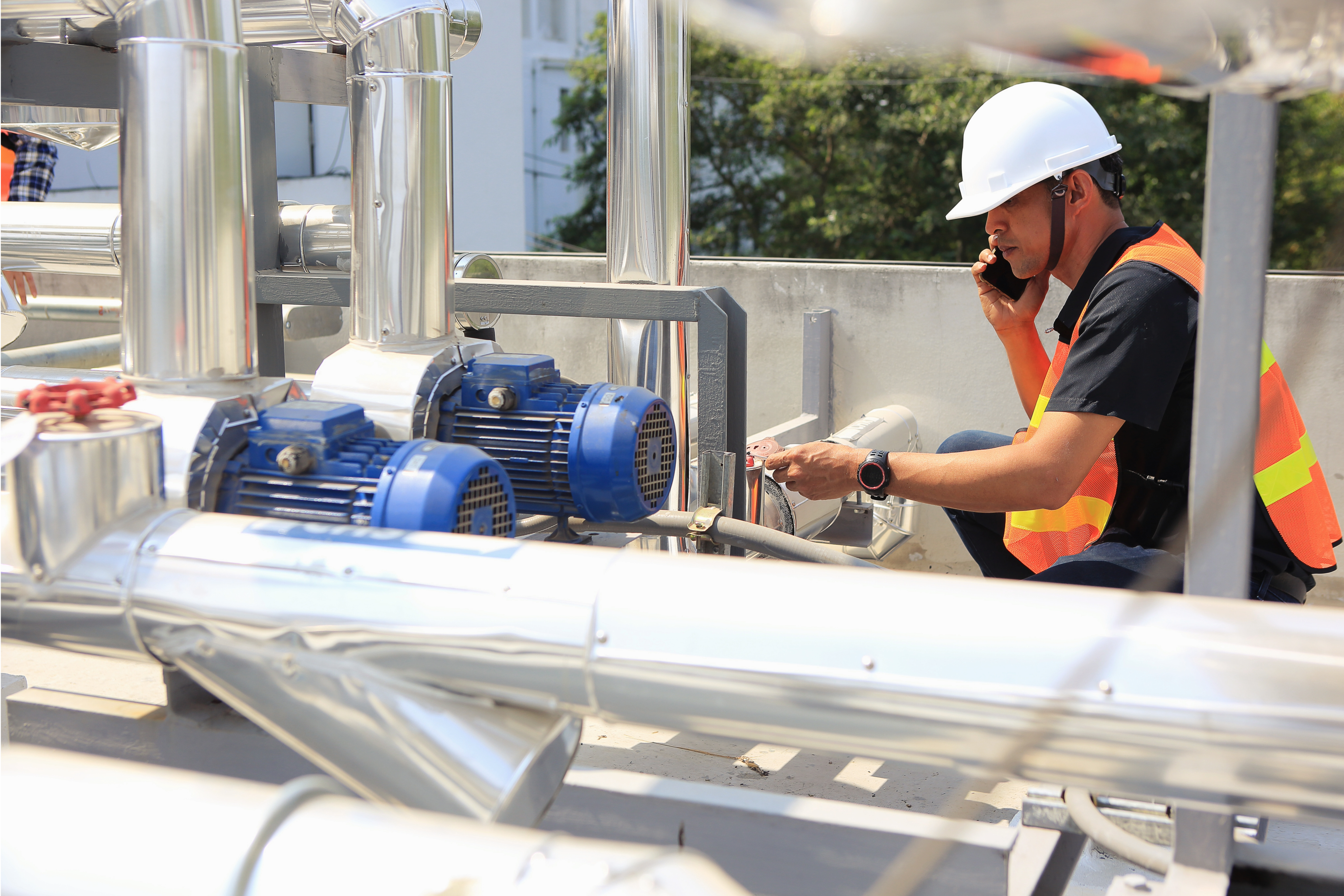
Process controls are critical for the success and safety of industrial processes. Having the capabilities to monitor and adjust processes on the fly means a process that is less prone to runaway deviations and safety issues.
Today we will discuss process control valves and look at a high-level overview of the things that need to be considered with any new or existing application.
Some of the other key factors that need to be considered for any new or updated control valve installation are:
Control Valve Selection
Control valves are key equipment in controlling process output, efficiency, and safety. Control valves come in many types and sizes depending on the application. So, specifying that product is critical. Due to the importance of this, working with a professional to select the right product for your application is a necessity.
How can a knowledgeable process engineer help you in this regard? Well, control valve selection is important for:
- The type of application
- Considering pressure drop across the valve (which can impact energy use)
- Durability over time (materials like steel or ceramics may be used depending on expected lifespan)
- Overall cost-effectiveness
All of these factors come into play when considering all options and requirements of your process.
Alongside this is considering how your control valve will operate and, critically, the control valve actuation. Control valve actuation is the process of opening and closing a control valve. Control valves can be actuated in several different ways, like:
Manual Control Valves – These operate by an operator manually turning the handle, which opens or closes the flow through the pipeline it is connected to.
Pneumatic Control Valves – These are operated with compressed air, where a pneumatic actuator is used to open and close the valve.
Electric Control Valves – These operate by an electric solenoid that opens or closes a mechanical spool inside of it, controlling flow through the pipeline.
These are just a few common examples. Control valves can also be actuated in other ways not listed here for various industrial processes and settings that require.
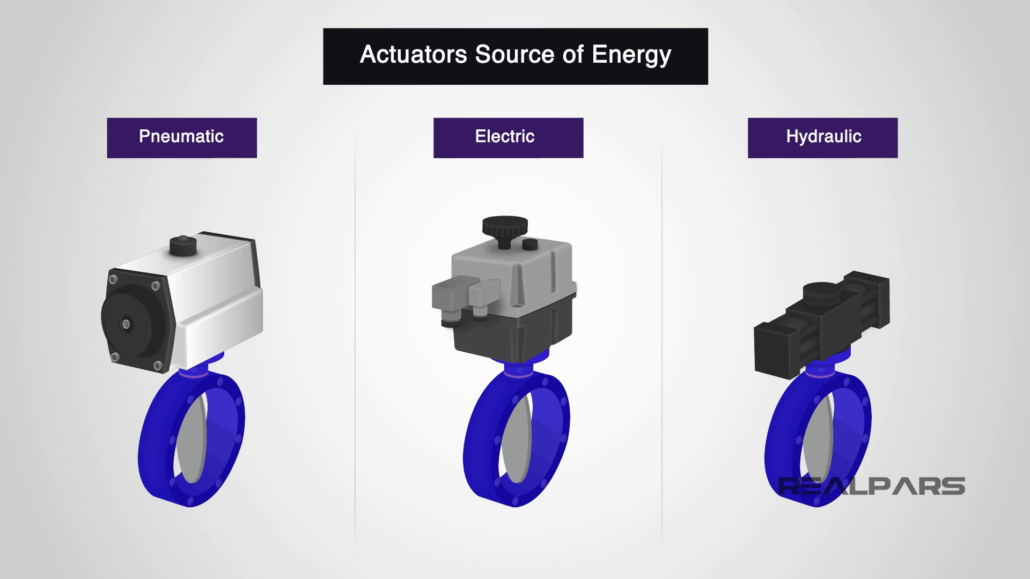
Control Valve Sizing
Control valve sizing is important because you want to make sure you are getting the correct type and size of valve for your process. Selecting the wrong valve size can lead to all sorts of issues down the line. So, it is important to do your research before making a purchase.
A control valve size is selected according to the diameter of the pipeline that it will be placed in. Control valves can handle a range of pressures and flow rates, but if you are not sure what your process requires then talking to a professional will make for an easier installation.
Control Valve Positioning
This is extremely important because control valve positioning impacts efficiency greatly when considering the rest of the process. Control valves can be placed in a number of different positions, and it is important to know where your valve needs to go before making any decisions.
In general, control valves are put into one of three categories based on their positioning: upstream, downstream, or parallel. Upstream control valves are those that are installed between the process and the rest of the process piping. Downstream control valves are installed after your main flow is complete, whereas parallel control valves connect to both sides of a pipeline (and can be used for balancing purposes).
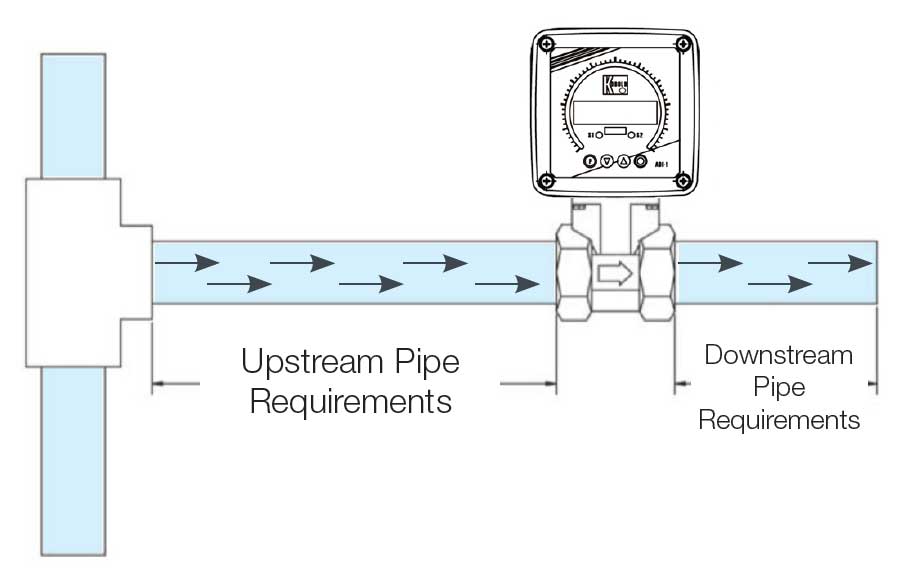
Control Valve Installation
Once you have selected the proper valves, you need to ensure that they are installed correctly. This means considering things like piping requirements, material compatibility, and operating conditions. Installing a control valve improperly can negate any benefits that it might provide, so getting this right is critical.
A good control valve installer will make sure that the process is up to code with local and national regulations and make sure that you are getting the proper product. Control valves come in many types of materials depending on the application so working with an experienced installer can make all the difference when it comes to valve functionality over time.
Control Valve Operation and Maintenance
Properly operating and maintaining a control valve is essential for ensuring its longevity and optimal performance. Control valves require periodic maintenance in order to keep them running smoothly and efficiently.
This maintenance typically includes cleaning the valve, checking for any leaks or damage, and lubricating moving parts as needed. A control valve that is not properly maintained can lead to a variety of issues and costs down the line. It is important to make sure you are taking care of your equipment.
A control valve operator will make sure that your process is functioning properly and check for leaks, blockages, or any other issues related to the valve. These devices are used in several different settings, from chemical plants to manufacturing facilities. It’s important that your experienced professionals know how to get results specific to your application and maintain that piece of valuable equipment.
In Conclusion
This has been a brief wrap-up of key considerations for any control valve application. In summary, we want to emphasize why it’s important to not leave such process-critical equipment up to chance. Always leverage the experts, understand the process, and let the valve do its job. Control valves can provide great benefits when used correctly in an industrial setting—but only if you select, install, and operate them properly!
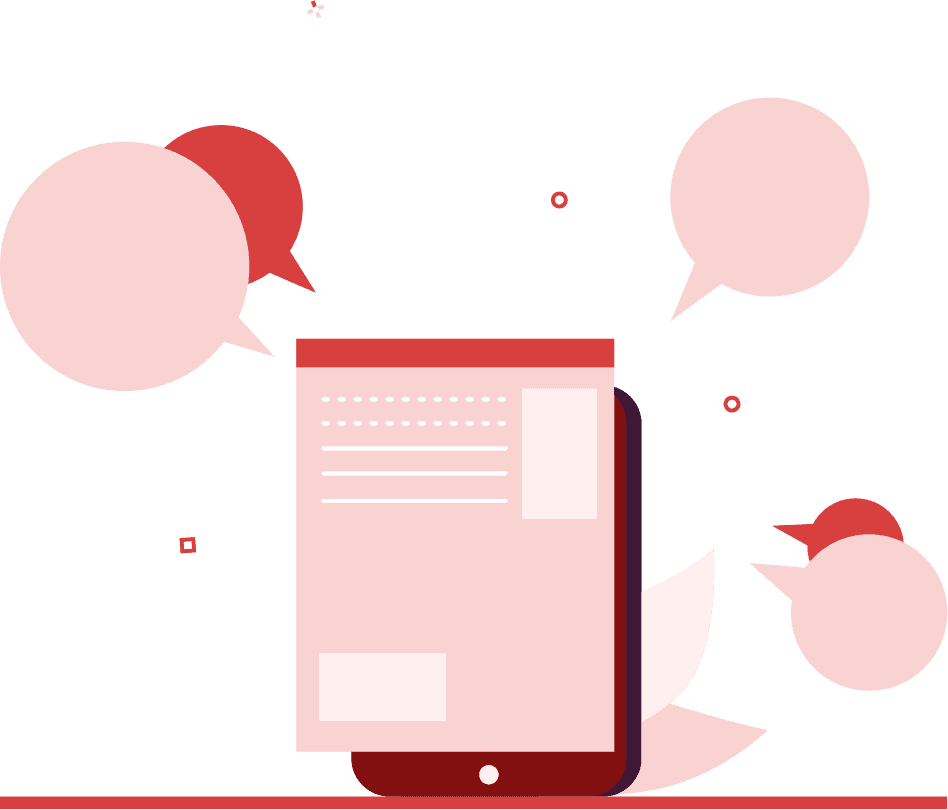
Get More Information on control valve and process maintenance!
To learn more about control valves and process maintenance, contact us today!
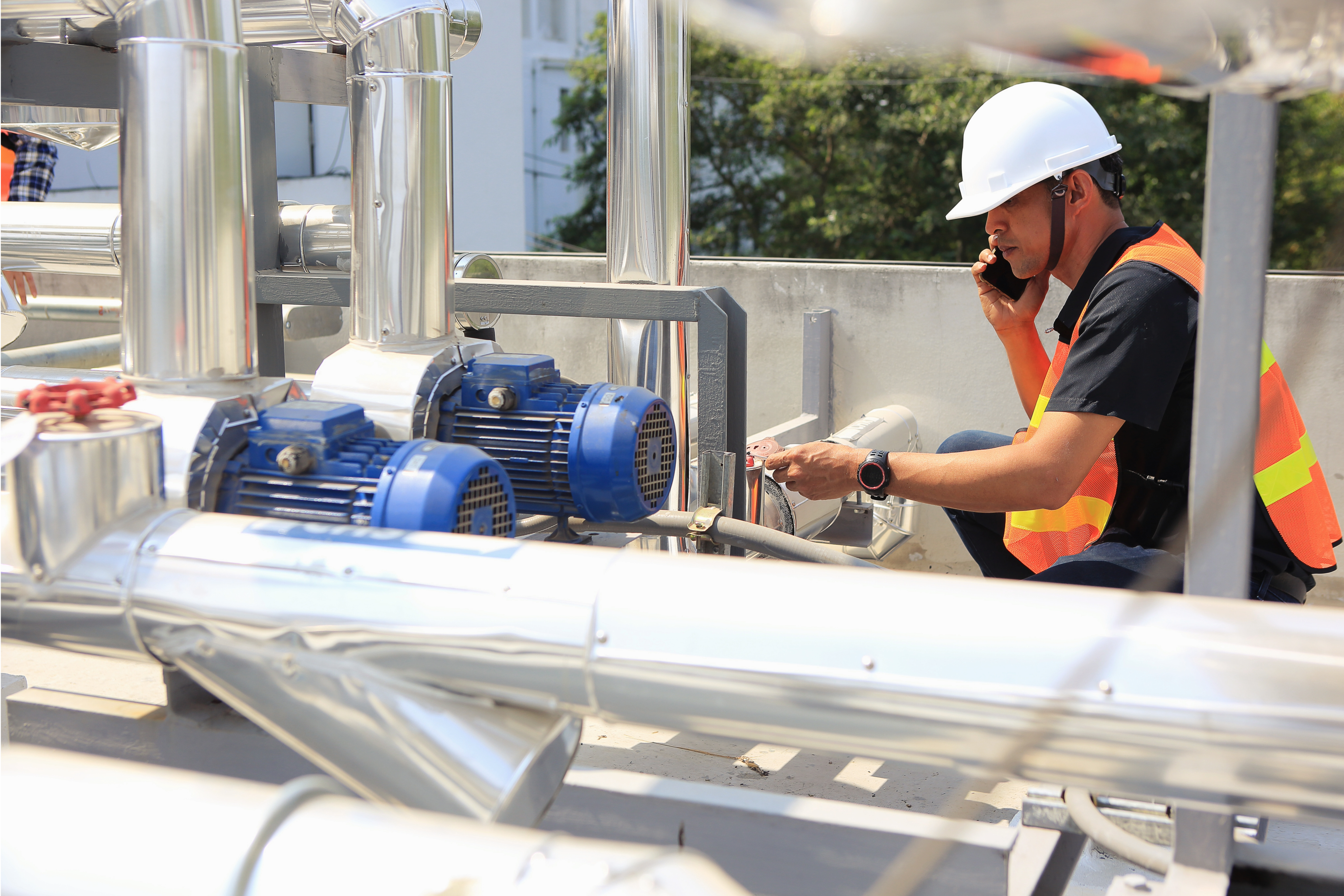
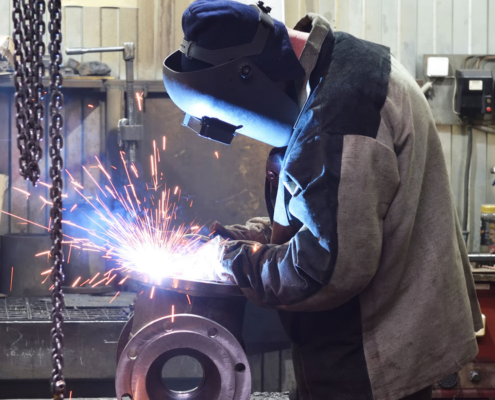
Common Control Valve Problems and How to Fix Them
Control Valves, Industrial Valves, Valve Maintenance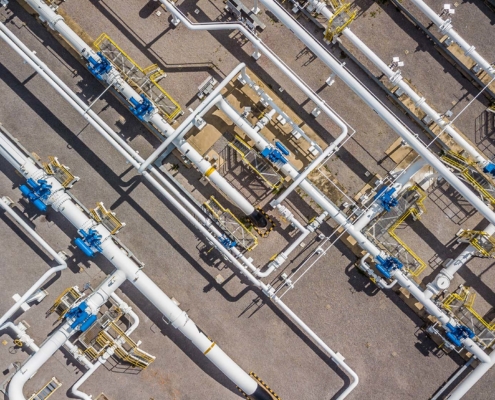