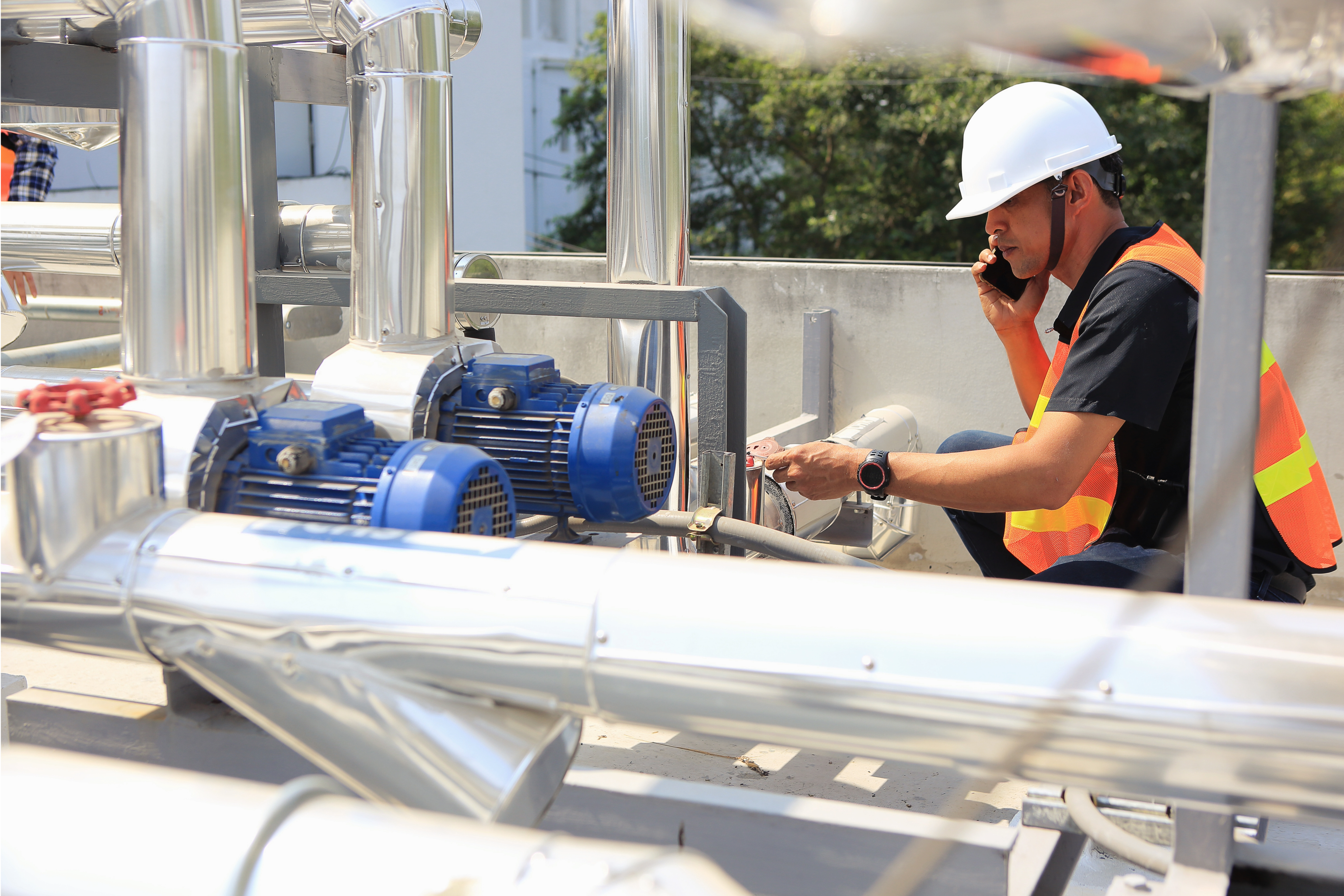

Pressure relief valves are exactly what their name suggests. These valves are designed to maintain a system at or below a safe pressure. When pressure in the system starts to exceed the safety setpoint, the valve relieves the system. The valves open up to atmosphere, recycle stream, bypass stream, or other manners of siphoning the excess material.
Now you understand the general purpose of a PRV (pressure relief valve). So, let’s take a closer look at different types of PRVs, their applications, and how to select one for your process.
When is a Pressure Relief Valve Used?
Under ideal circumstances, a PRV in line with your overall process does not do a whole lot. Regardless, these devices are desirable in cases related to:
- You have pressure-sensitive equipment in the system.
- The process is pressure-sensitive due to construction materials and other process conditions.
- Personnel safety.
- Overpressure could release fluids into the environment that are hazardous and need regulation.
Most industrial processes fall under some or all these restrictions. Simply put, effective use of PRVs in your process:
- Protects equipment and personnel.
- Helps equipment in line operate effectively.
- Helps mitigate environmental and safety concerns.
- Prevents downtime.
As such, PRVs are critical in even the simplest processes. Their effectiveness is necessary in processes involving harsh chemicals and hazardous conditions.
The image above is a typical P&ID (Piping and Instrumentation Diagram). This one shows a PRV situated to support the system it is built into.
Types of Pressure Relief Valves
There are a variety of PRVs that differ in their use case and functionality. We are focusing on their use in industrial applications. Although, they are commonly used in everyday plumbing applications as well. (They don’t call chemical engineering an advanced plumbing degree for nothing.)
First, a quick distinction between the types of PRVs:
- A RV (Relief Valve) gradually opens and acts as a pressure modulating device at times. RVs are used in processes with non-compressible media.
- An SV (Safety Valve) is a strict open/close device. It opens rapidly and releases overpressure fluids for immediate relief. This ensures safety of the process environment and operators. SVs are used in processes with compressible media.
- An SRV (Safety Relief Valve) is a PRV designed for use with both RV and SV applications.
Despite the similar names, the three devices are quite different.
Direct Acting Relief Valves, Safety Valves, or Safety Relief Valves
Direct operating valves are self-operating. Unlike other types, they do not require an upstream sensing line to function properly. Using a bellow or diaphragm, these react directly to sensed pressure. Then, it opens or closes according to the system pressure and the valve’s set point.
Pilot-Operated Safety Relief Valves
Pilot valves use a sensing line to the pilot which controls the operations of the main valve. For more information on how pilot valves work and their purpose, check out our recent blog here.
Modulating Pressure Relief Valves
These valves modulate according to overpressure. As opposed to a relief device that snaps open, these gradually open. Then, they seat themselves dependent on the degree of overpressure.
A modular relief valve can be desirable for a variety of reasons. For example: process conditions where sudden flow through a set orifice size might cause issues to the process. The modulation can prevent sudden phase change in the fluid or knocking (cavitation) in the device itself. Another example is where limiting emissions are critical. A modulating valve will only relieve the minimum amount of media to restore the system pressure to safe conditions. By utilizing this type of valve, the emissions are limited to the minimum amount.
Don’t let this all confuse you. Understanding your process, safety requirements, and regulations is a great start. A good company will work with your process to specify a perfect fitting solution. As an example, you can often buy models where a modulating pilot configuration is optional. Yet, this is dependent on the equipment manufacturer and distributor you are working with.
Rupture Discs, Emergency Relief Valves, and Hatches
In technical terms, rupture discs are not valves. Regardless, they fit well in this category and deserve consideration. A rupture disc is a simple device. When pressure reaches the specified overpressure setting, the rupture disc bursts.
This is often a “last resort” item. When other preventative measures fail, rupture discs can protect critical and expensive equipment. If you don’t expect overpressure situations to occur often, a rupture disc may be a cost-effective solution.
Emergency relief valves and hatches are often used on vessels. These can protect against rupture of the vessel in cases of overpressure. Like a rupture disc, it ensures relief capability when pressure exceeds expectations. Hatches are often specified for gaining access to tank contents, gauges, and sampling.
Venting It All Off
That’s a lot of information to take in. You may be feeling like you could use a PRV device right now. Trained, educated professionals can help you select the proper equipment.
The main takeaways from today:
The industrial processing world…
- Is full of harsh conditions
- Has picky process equipment
- Has strict environment and safety regulations
Valuable fluids and huge capital expenditures create these processes. So, overpressure in a system can cause costly shutdowns and expensive equipment failure. Furthermore, damage can cause harm to the people who run these processes around the clock.
Proper specification, implementation, and maintenance of pressure relief valves is critical. Your process, business, and safety all benefit from doing things right.
As you learned today, there are many options to choose from. Custom, tailored solutions work well to meet all your needs. In conclusion, there is no reason to take shortcuts for such an important part of your plant.
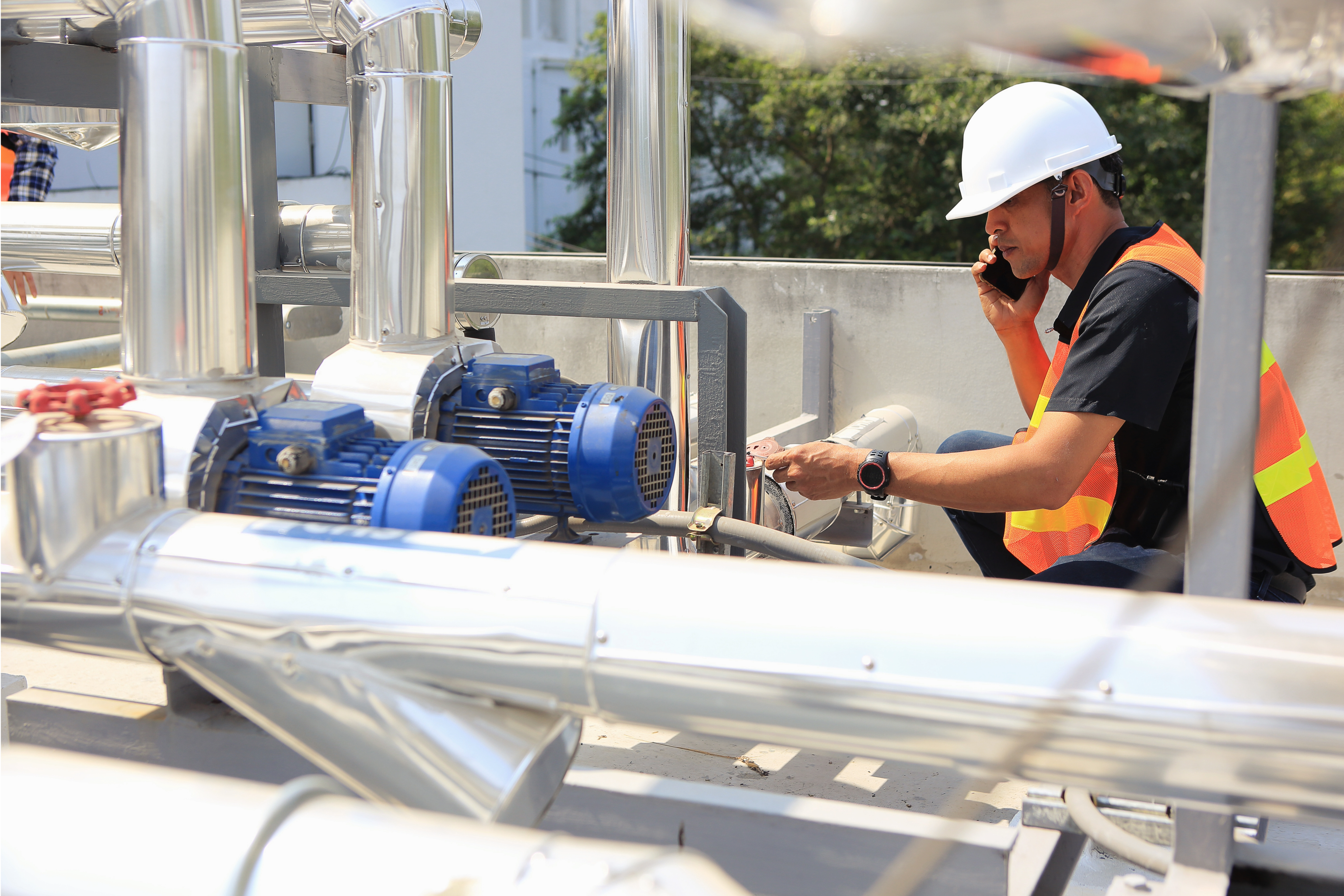
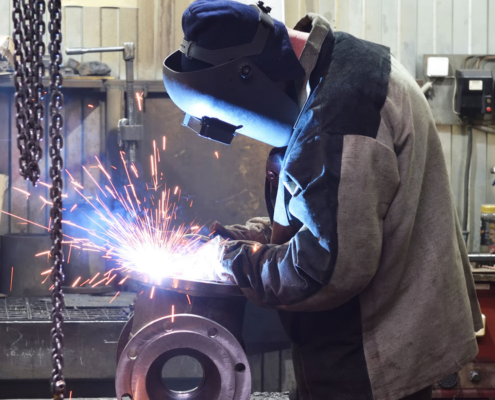
Common Control Valve Problems and How to Fix Them
Control Valves, Industrial Valves, Valve Maintenance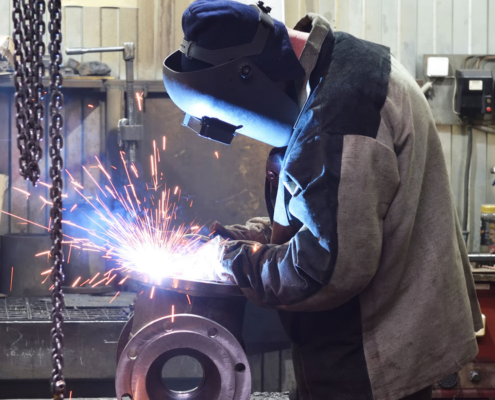