Actuators are the equipment that give advanced flow control valves their dynamic ability. Without strong actuation technology, the engineering and money spent on top-of-the-line control valves risk being wasted.
An actuator, simply put, is the device that controls the movement of a relevant system. In this post, we will be specifically discussing the actuation of control valves. In many cases, control valves need precise movements. Furthermore, these control systems may be responsible for the critical flow of valuable chemicals under harsh conditions. In these types of scenarios, actuators play can play an important role.
Today, we will briefly cover common forms of control valve actuators, some unique technologies developed to refine them, and their applications and use conditions. While this won’t be an exhaustive list of actuation technology, we will cover the fundamental applications of actuators in the world of fluid process controls. Let’s get started.
Types of Control Valve Actuators
There are two main types of actuation technologies that we will be covering, under which further distinctions separate their ideal use cases. The two are:
- Linear Actuators
- Rotary Actuators
For each of these actuator types, they can be operated by a few different “power” sources, like:
- Hydraulic Actuators
- Electric Actuators
- Pneumatic Actuators
We will also be covering a unique combination of the latter, called Electraulic™ actuation (also known as electro-hydraulic.) By exploring Electraulic™ actuation, we will see how combining basic actuation technologies give us the “best of both worlds” and improve overall performance.
Linear Actuators
A linear actuator, as the name implies, moves the control valve in a linear fashion. This straightforward, back and forth motion gives a linear actuator some strong benefits:
- Their simplicity in design makes them versatile and reliable,
- Less complexity in range of motion means higher accuracy and repeatability,
- A longer life span for the equipment, and more relaxed maintenance requirements.
As you can gather, it’s often a very easy decision to opt for a linear motion actuator. However, let’s look at why you may have to consider another option.
Rotary Actuators
Fortunately, just like the linear actuator, the rotary actuator doesn’t have any extra surprises. It too operates according to its title: the actuator moves in a rotating fashion. Some reasons you may choose a rotary actuator may be any number of the following:
- Rotary motion is required for a specific application,
- High torque capabilities are needed due to process flow forces of a higher magnitude,
- A wide variety of diameters are present in the valves in use,
- There are no restrictions in the range of motion.
Rotary actuators are sometimes necessary in a given application, but they also have desirable benefits where a linear actuator may be functional as well.
Powering Actuators
We’ve now covered the basic motion of linear and rotary actuators, as well as their ideal applications. Now, let’s look at the actual method of powering the motion of these actuators. There are varying actuator types in varying industries, but we will cover the essential few commonly involved in process flow controls:
- Hydraulic
- Electric
- Pneumatic
Additionally, we will touch on the specific hybrid of the latter, called Electraulic™ actuation.
Hydraulic Actuators
Hydraulic actuators are powered by fluid, typically oil. Oil is often used in these applications due to its incompressible nature, and its ability to transfer large amount of force in relatively small volumes. This is referred to as a high force-to-size ration. A hydraulic actuator is robust and reliable but may come with a high up-front cost due to its benefits. Because their pressurized is so critical, it’s important to ensure regular maintenance to prevent any leakage.
Electric Actuators
Electric Actuators are more direct in their transfer of electric energy into torque, which is used to operate the device. Here, electricity is used to move an electric motor. Their simplistic design and lack of operating fluids makes them an appealing choice. There is less worry involved when it comes to maintenance and clean up of leakages. This does not, however, mean they are an easy fix in terms of maintenance. If they do malfunction, it can have its own set of problems. Regardless, depending on your team, fixing an electric motor may be more or less daunting than fixing a hydraulic fluid leak.
Pneumatic Actuators
Pneumatic Actuators are similar to hydraulic actuators, as oil and air can both be considered fluids. However, the compressed air in these actuators is unable to translate as much force as hydraulic fluid. These actuators are often utilized for applications with lower force requirements. Because they only require compressed air, these devices often fit into existing operations quickly and easily. They are a simple and economic choice, which can be very appealing in some situations.
Electraulic™ Actuators
Electraulic™ actuation technology is a unique combination of all the above technologies. These actuators have hydraulic and electric systems. This means they have the power delivery of hydraulics, and they have the control and simplicity of electric actuators. Essentially, the combination of technologies brings the benefits of each, while hedging against the drawbacks of either device.
These Electraulic™ actuators, manufactured by REXA, come in linear, rotary, and damper drive configurations. Their hydraulic components are self-contained, meaning the end use isn’t required to have their own hydraulic systems on site to support their operation.
Wrapping It Up
We’ve now seen a quick overview of actuator technology used in the process control industry. We’ve seen how these devices operate in linear and rotary movements, as well as the sources that drive them. The variety in system forces can have a drastic impact on how effectively process flows are controlled. We hope that all this information gives you a more confident understanding of actuator technologies. And as always, remember to consult with your product experts to ensure you find the best fit for your needs.
Other Resources
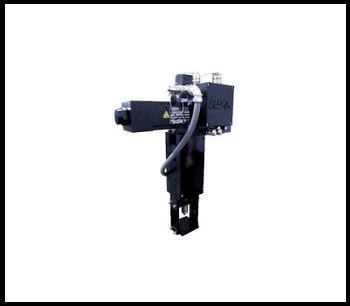
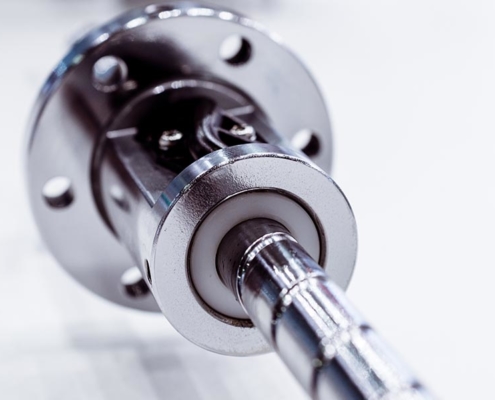